Injection molding machine is a special equipment that combines the thermal processing characteristics of plastics with the principle of molten die-casting of metals. The original plunger injection molding machine, the pre-plasticizing screw injection molding machine was developed in the late 1940s. Since then, the focus of development has been mainly on pre-plasticizing screw injection molding machines, and advanced forms such as twin-screw and exhaust type have appeared in the future.
In 1980, France made the largest screw injection molding machine in the world at that time, with an injection capacity of 170kg. From the 1980s to recent years, the development of injection molding machines has mainly focused on several aspects: the application of fine automatic control systems and various auxiliary equipment in automatic molding; the coordination of precision machinery and high-performance hydraulic systems; various special The development of injection molding machine and computer-aided design analyze the plastic flow of complex shape parts to determine the best injection molding conditions; the application of various energy-saving technologies in injection molding machines.
The working principle of injection molding machine
Injection molding machine is referred to as injection molding machine. Injection molding uses the thermophysical properties of plastic to add materials from the hopper into the barrel. The outside of the barrel is heated by a heating ring to melt the material. The barrel is equipped with an external power motor. Screw, the material is gradually plasticized, melted and homogenized under the double action of screw shearing. When the screw rotates, the material will push the melted material to the screw head under the action of the friction force and shearing force of the falling groove. At the same time, the screw retreats under the reaction of the material, so that the head of the screw forms a storage space and completes the plasticization process. Then, under the action of the injection cylinder piston, the screw passes the molten material in the storage chamber at high speed and high pressure. The nozzle is injected into the cavity of the mold. After the molten material in the cavity is pressure-maintained, cooled, solidified and shaped, the mold opens the mold under the action of the clamping mechanism, and the shaped product is ejected from the top of the mold through the ejector device.
The composition of the injection molding machine
According to the requirements of the injection molding process, the injection molding machine is a machine with strong mechanical and electrical integration, which is mainly composed of injection parts, mold clamping parts, racks, hydraulic systems, heating systems, control systems, and feeding devices.
At present, the common injection molding devices are single-cylinder and double-cylinder.
There are two types of plasticizing parts: plunger type and screw type. During the continuous pushing process of the rotating screw, the plastic changes its physical state, and is finally injected into the mold cavity in a molten state. Therefore, the plasticizing component is the core component for uniform plasticizing and quantitative injection.
Main Features:
One.The Lock Section
1.Arch template, effectively protects the mould, especially suitable for big template with small mold.
2.The electric ruler is installed on the crosshead, the position is more precise.
3.The front connecting rod uses connected structure, increases the rod strength, and easy for assembly
4.The connected tail-board stills itself with big lock shaft, improves tail-board strength, and ensures zero abrasion of the tail-board, easy for maintenance.
5.Connected movable plate, improves its rigidity and reduces deformation
6.Connected thrust bearing, improves its strength and stills itself with small lock shaft, ensures zero abrasion.
7.Arch template fully complies with mechanical property, largely improves template strength.
8.More reasonable toggle design, speeds and stabilizes mold opening and closing.
9.Adjustable movable plate mounting plate, makes the installation easier.
10.Mixed design of T-shape groove and die hole, increases universality of the mold.
Two.The Injection Section.
1.Bridge type support, improves injection smoothness.
2.Longer length-diameter ratio screw design, improves plasticizing effect.
3.Double seal structure, ensures no oil leakage.
4.Withhold type press plate, easy for debugging and assembly.
5.Bijection structure, improves stability.
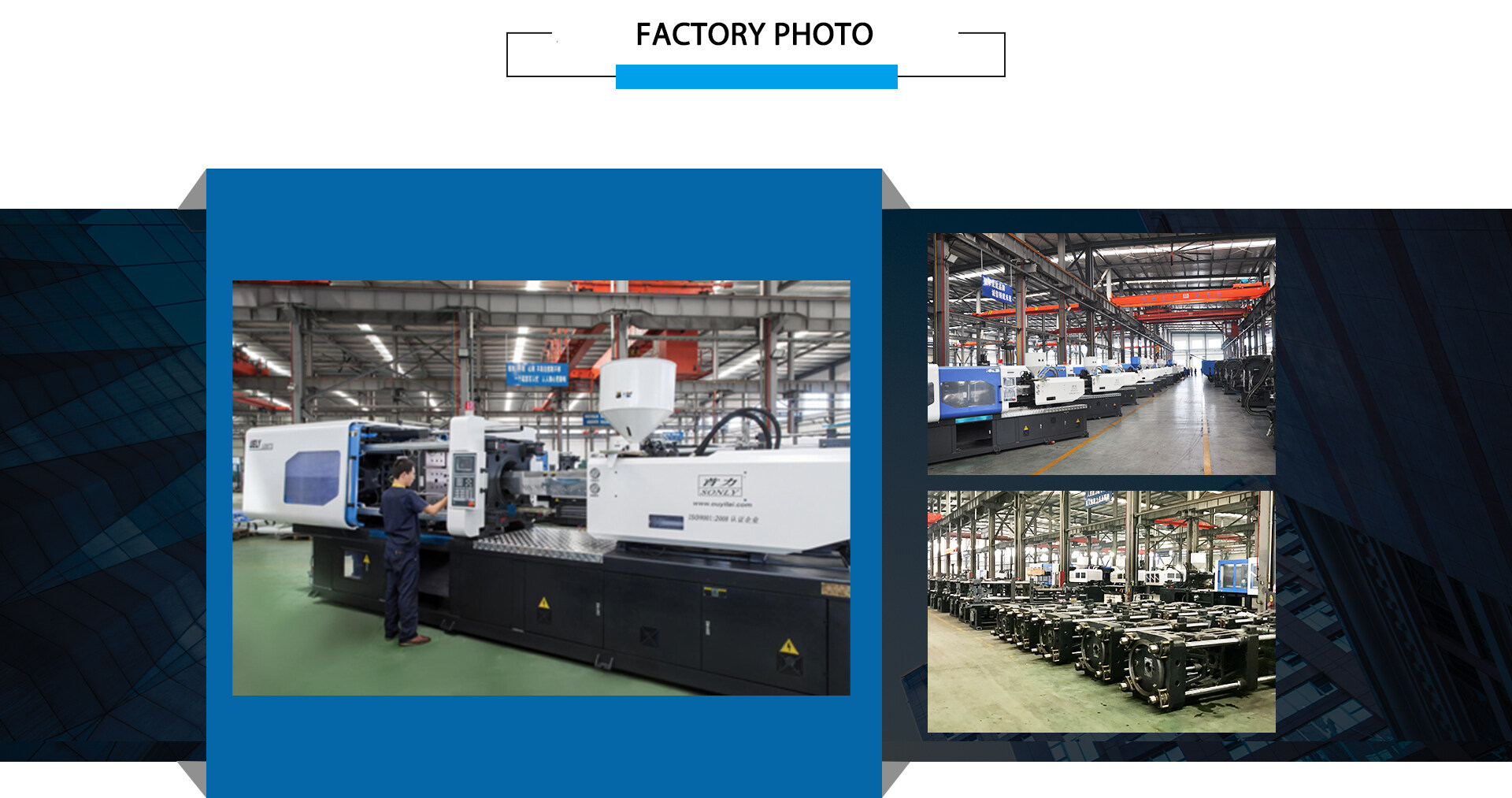
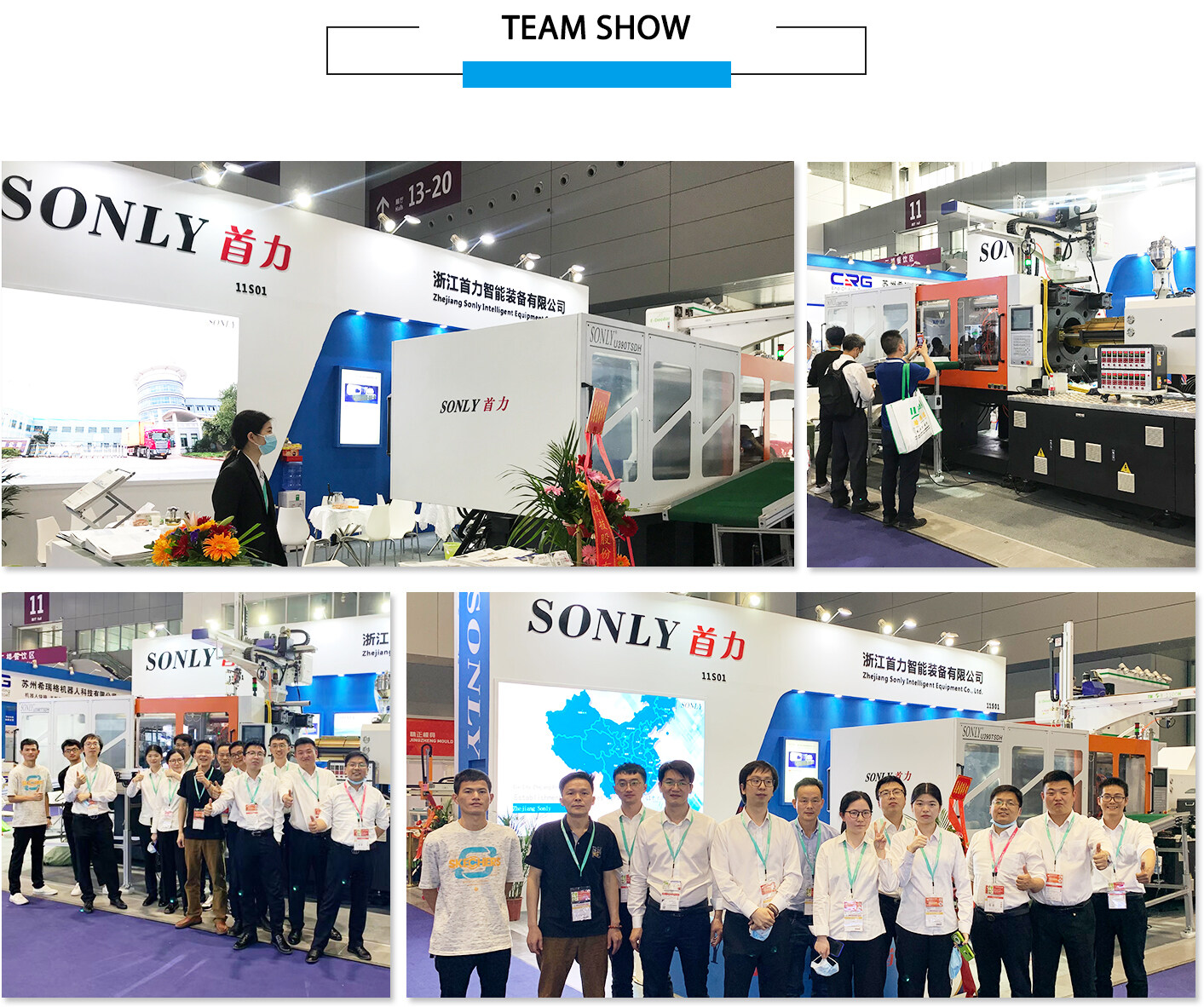
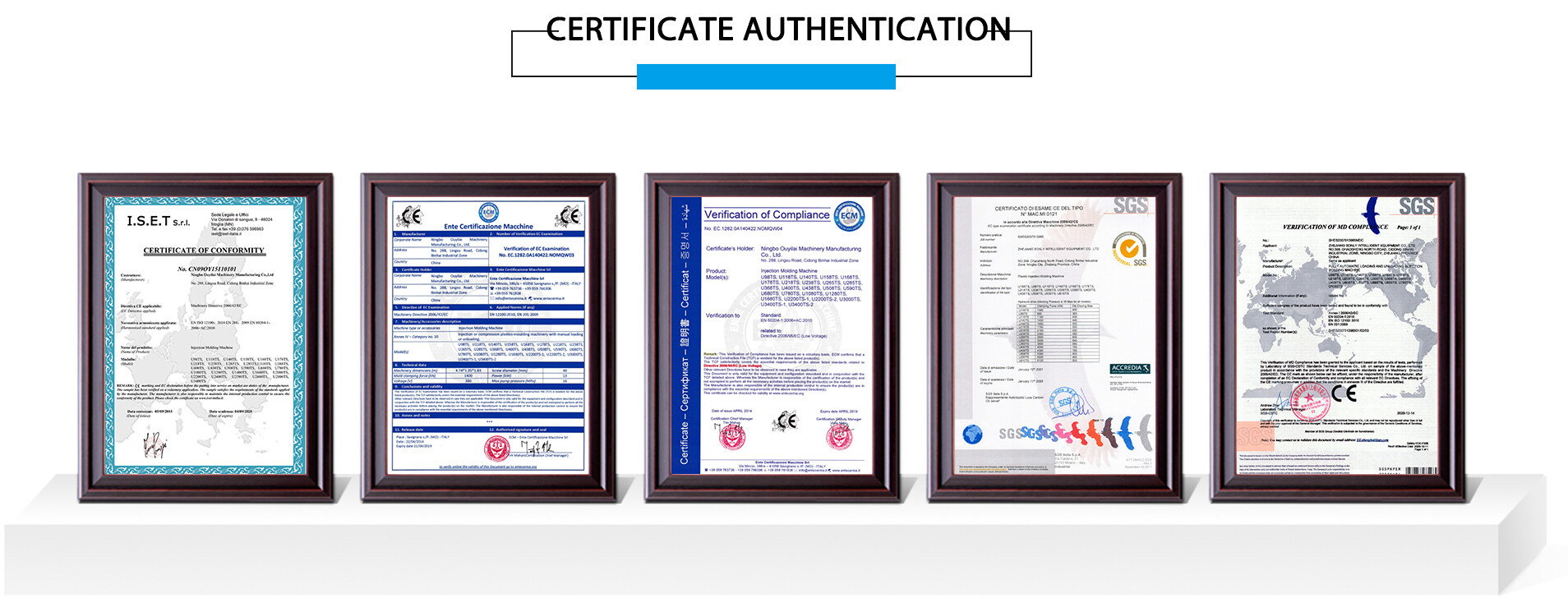
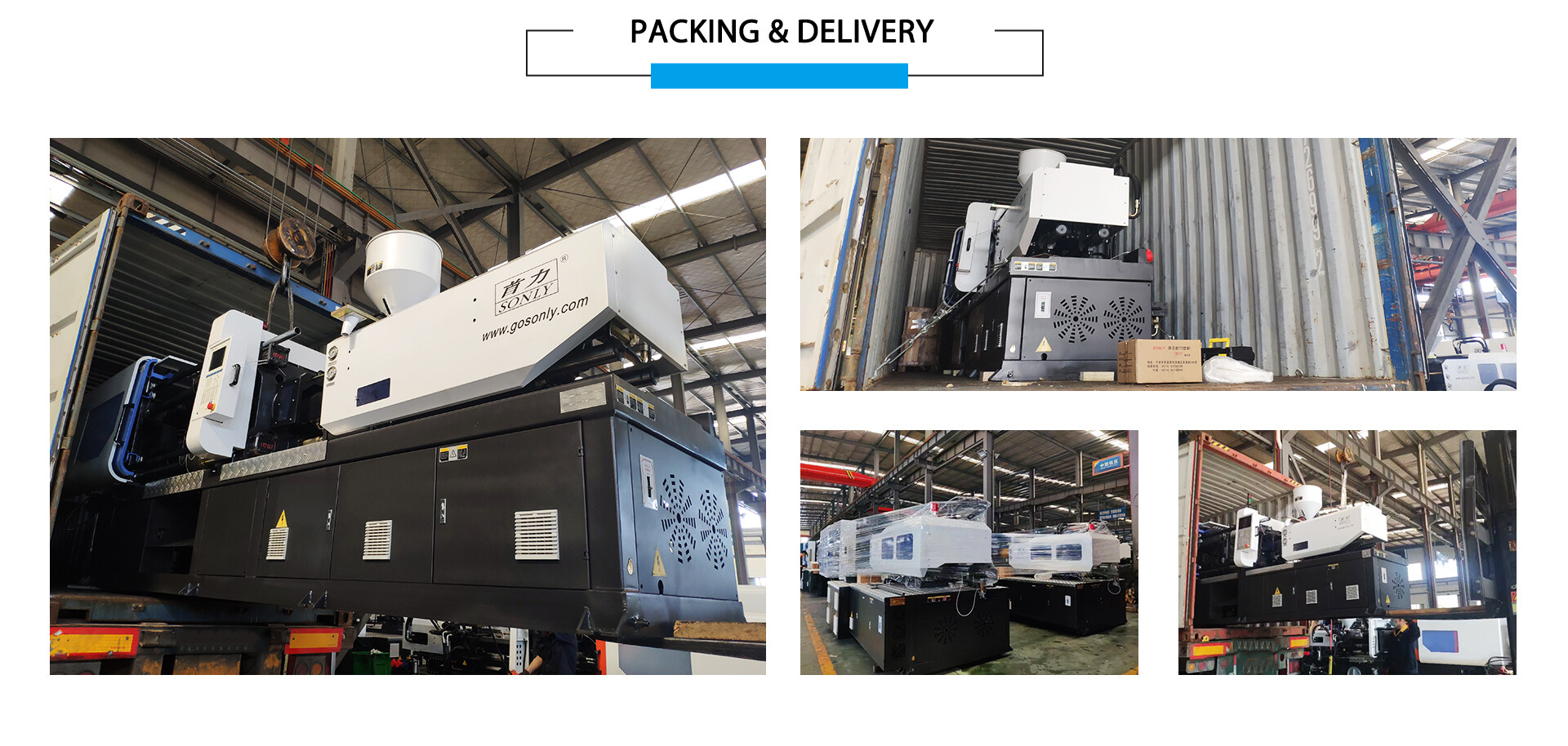